|
3. Development of basic technologies
The Kunitachi institute has promoted research and development centering on the durability of superconducting magnets and ground coils over long periods, and has developed and tested a device to locate the point of ground fault in feeding circuits to support quick recovery operation.
(1) Verification of superconducting magnet durability
In one of the most important areas for the commercialization of the superconducting magnetic levitation railway system, the RTRI verified the durability of a superconducting magnet over a period equivalent to the lifespan required for revenue service.
The superconducting magnet is subjected to load fluctuations caused by magnetization/demagnetization, heat cycles and vibration during running. Durability over a period equivalent to the service lifespan taking into account the former two factors has been verified through running tests on the Yamanashi test line. To verify the effects of vibration during running, however, the frequency of loading was insufficient in past running tests. To compensate for this shortage, the RTRI implemented a superconducting magnet excitation bench test (Fig. 9).
The effect of vibration on the superconducting magnet during running is the greatest at the resonance frequency, with the whole magnet subjected to a vertical torsional force from levitation coils and to a lateral bending force from propulsion coils. Since the durability of superconducting coils, load supporting members and other major components had already been verified by unit tests, the RTRI investigated the durability against vibration of the superconducting magnet as a whole including low-temperature piping. For this purpose, the RTRI performed exciting tests on levitation coils in a 60-degree pitch 4-square grid arrangement and on propulsion coils in 120-degree pitch single-layer arrangement. This simulated the vibration during actual running to a cumulative frequency equivalent to that expected during 15 years of operation on revenue service lines. Results showed no abnormalities in the degree of vacuum in the vacuum tank or low temperature piping, and no changes over time were observed in the vibration modes of the different parts. Summarizing the results of the running and element technology tests, the RTRI was able to confirm that the superconducting magnet had the durability required for operation on revenue service lines (Fig. 10).
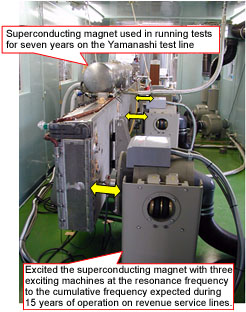
Fig. 9 Durability test apparatus | 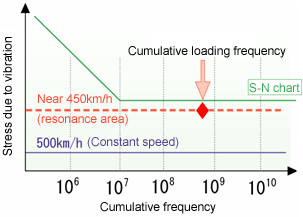
Fig. 10 Cumulative frequency of vibration loading in the durability verification test |
|